The conventional Machining Process, also known as traditional machining in manufacturing, this process involves the use of cutting tools to remove excess materials from a workpiece on direct contact. Furthermore, this machining operation occurs when the cutting tool directly interacts with the workpiece.
There are 7 types of conventional machining, and they include:
1. Turning
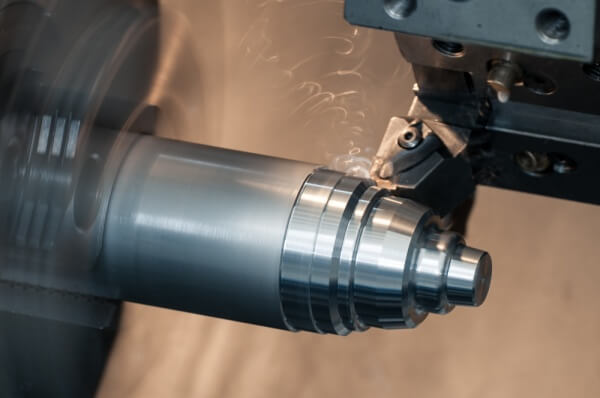
In the turning process, the cutting tool remains stationary while the workpiece rotates. Furthermore, it is a lathe operation and involves the removal of excess material from a workpiece with the aid of a cutting tool. Besides, the cutting tool works along two axes of motion, creating cuts with precise width and depth.
Additionally, the turning process works great for machining the interior or exterior part of a material. Turning performed on the material exterior part is known as facing, while that done on the inside is known as boring.
2. Milling
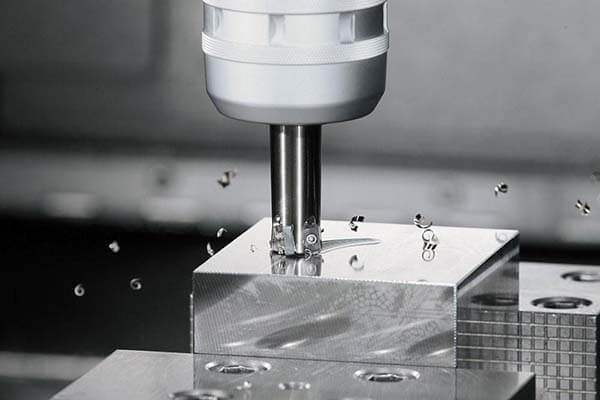
Milling is a machining process that involves the use of rotating cutters to remove material from a workpiece. Furthermore, there are two main types of milling operations; face milling and slab milling.
Face milling is a machining manufacturing process used for smoothening or flattening the surface of workpieces. Conversely, slab milling is ideal for machining a wide flat surface. It also involves making planar cuts across a workpiece’s surface using the mill cutter’s peripheral edges.
Besides, this is one of the types of machining that involves a complex process and often requires a variety of special cutters to perform tasks. However, machining companies like Seicenc offer 3-axis and 5-axis CNC milling services, with milled parts having a tolerance of up to 0.005mm.
3. Drilling
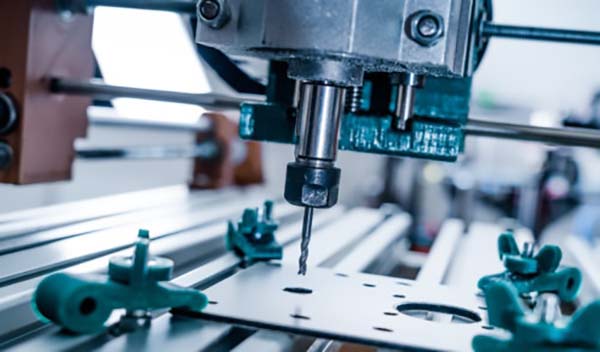
Drilling involves using drill bits (multi-point cutting tools) to produce cylindrical holes in solid materials. Furthermore, drill bits used for this procedure feature two spiral channels. These channels, also known as flutes, evacuate the swarf or chips out of the hole as the drill bit progresses into the material.
Additionally, the holes created by this drill press often aid part assembly. Besides, drilling is applied first before tapping, reaming, or boring to create threaded holes or bring the dimension of a hole within an acceptable tolerance. This makes this operation one of the most important out of the other types of the machining process.
4. Grinding
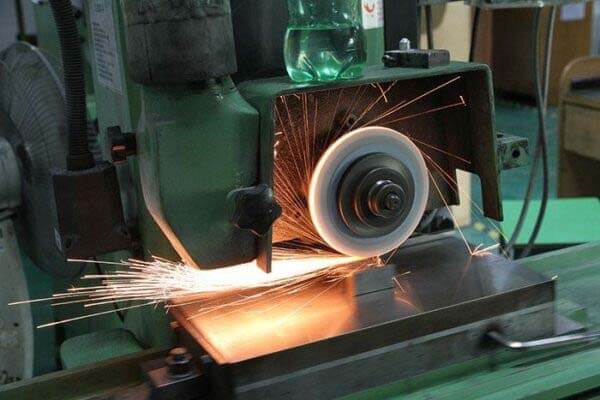
Grinding is one of the types of machining process ideal for improving the finish on a machined part’s surface and tightening its tolerance. Furthermore, the process produces parts with identical shapes, finishes, and sizes. It is also the first step in further finishing operations like honing, lapping and superfinishing.
Additionally, there are two main types of grinders; Surface grinders and Cylindrical grinders. Surface grinders remove small amounts of materials from flat surfaces, but cylindrical grinders remove materials from cylindrical shapes.
5. Sawing
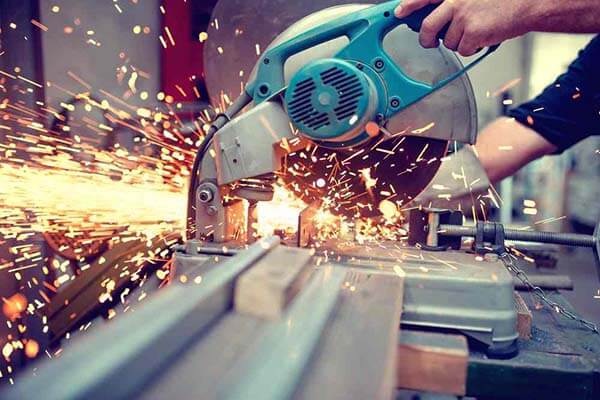
Sawing aims to create shorter lengths from extruded shapes, bars, and other materials, performed by cut-off machines. Furthermore, there are different cut-off machines engineers use for sawing, including; power hack saws, circular saws, and abrasive wheel saws.
Besides, the saw band speed for sawing depends on the material. For instance, softer materials like aluminum alloys require a cutting speed of 1000 fpm or more. On the other hand, some high-temperature alloys require a slower cutting speed of 30fpm.
6. Broaching
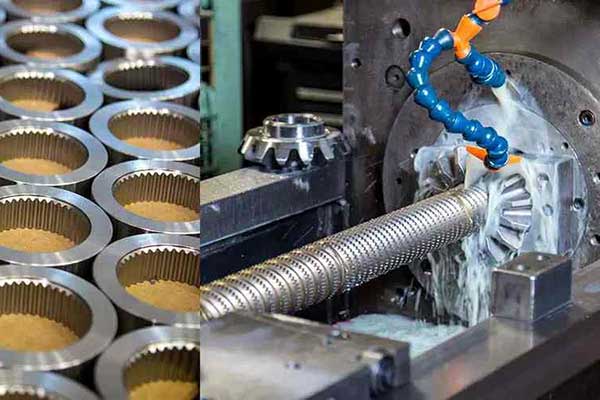
Broaching involves using a broach to produce square holes, spline holes, keyways, and other shapes. Furthermore, a broach is a tool with many teeth arranged in sequence, similar to a file. However, it differs from a file in that a broach has uneven teeth, while a file consists of even-sized teeth.
There are two types of broaching; pull broaching and push broaching. vertical press-type machines are ideal for use in push broaching, while vertical or horizontal press-type machines are ideal for use in pull broaching.
Besides, when pulled or pushed past a surface or through a leader hole, a broach takes a series of cuts with increasing depth. Also, the cutting speed of a broach is dependent on material strength. For instance, cutting speeds are often as high as 50 fpm for softer metals and as low as 5 fpm for metals of higher strength.
7. Planing
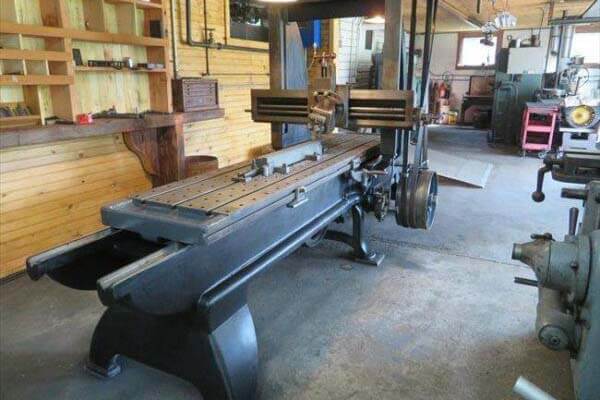
Planing is ideal for large flat surfaces especially surfaces that would still undergo scraping as a finishing method. Also, to reduce machining costs, manufacturers sometimes gang small parts together for simultaneous planning.
Let Seicenc boost your business today!
Seicenc has been in CNC machining industry for 12 years, let us provide you with high quality custom precision machined parts.
By the end of 2022, we have worked with more than 1,000 clients in more than 30 countries, and supplied them over 1 million unique parts.
Do not hesitate. Just contact us right now! We will give you an instant quotaion within one days!