The surface quality of auto parts can directly reflect the microcosmic and geometric errors of the part surface. Of course, surface roughness is also an important indicator of the reaction and an important basis for testing the surface quality of parts. Whether the choice is reasonable or not will directly affect the product quality and service life in the later stage, including the production process. The selection methods of the surface roughness of mechanical parts mainly include the calculation method, experiment method and analogy method.
In the design of mechanical parts, an analogy is widely used. This method is simple, effective and fast. The application of analogy requires sufficient reference materials. Various mechanical design manuals now provide comprehensive data and documentation. The comparison is the surface roughness corresponding to the tolerance class. Generally speaking, the smaller the dimensional tolerance requirements of mechanical parts, the smaller the surface roughness value of mechanical parts, but there is no fixed functional relationship between them. For example, the handles on some machinery and equipment, and the decorative parts on some equipment, surface requirements are very high, but the size requirements are very low. The use of cutting tools in the current machining industry also puts forward higher requirements for the improvement of technology. Not only requires long service life but also less pollution when cutting. Now follow us to see the high requirements of machining on cutting tools and the requirements of long life and low pollution.
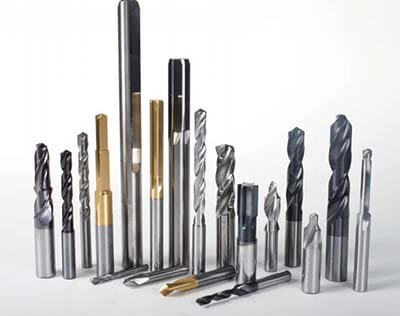
The requirements of CNC machining on cutting tools are mainly manifested in the following aspects:
1. With the development of science and technology, the mechanical processing industry has higher and higher requirements on the surface properties of materials. Especially in recent years, the rise of various precipitation technologies has made a breakthrough in the research and application of surface engineering technology. These technologies not only meet the requirements of mechanical properties but also play an important role in the fields of electromagnetism, optoelectronics, thermal blood imaging, optics, superconductors, and functional materials related to biological surfaces.
2. Surface engineering not only allows cheap metal materials to play greater advantages in terms of performance and size, but also has become an important means for various new coatings and thin film materials with great application potential.
3. The diversity of tools and the characteristics of their use state determine the difference in the choice of tool coating. Turning is different from drilling. The milling cutter should consider the characteristics of intermittent impact. The early development of the coating is mainly based on wear resistance, and the main index is to increase the hardness. During the machining process, the continuous friction between the tool and the workpiece will generate a lot of heat energy. To prevent the tool from overheating and deformation, affecting the machining accuracy and prolonging the service life, cutting fluid is usually used.
4. With the change in the mechanical processing industry level, almost all cutting tools are dry cutting. When the cutting fluid is not eliminated, try to ensure that it only contains rust inhibitor and does not contain organic matter, which can greatly reduce the recycling cost.
5. To solve some problems caused by reducing and eliminating cutting fluid, the tool coating should not only make the tool have a longer service life, but also have a self-lubricating function.
6. The emergence of diamond coatings shows significant advantages in the processing of certain materials. However, recent studies have proved that the hardness of diamond-like carbon coatings with SP2 structure can also reach 20-40 Gpa.
7. No catalytic effect with ferrous metals. It has a low coefficient of friction and good moisture resistance. Coolant cutting or dry cutting can be used. Compared to uncoated tools, its service life is doubled. Machining steel materials is no problem and is therefore of great interest to coating and tool manufacturers. Over time, these new diamond-like coatings will find wider use in cutting applications.
Let Seicenc boost your business today!
Seicenc has been in CNC machining industry for 12 years, let us provide you with high quality custom precision machined parts.
By the end of 2022, we have worked with more than 1,000 clients in more than 30 countries, and supplied them over 1 million unique parts.
Do not hesitate. Just contact us right now! We will give you an instant quotaion within one days!