CNC (Computer Numerical Control) machines are used to manufacture turned parts with very high precision. The machines are programmed to follow a set of instructions that tell them how to cut and shape the material. This process ensures that each part is exactly like the one before it, which is critical for precision engineering applications.
In CNC turning, a workpiece is rotated around a cutting tool to create precision parts. CNC turned parts are used in many industries, from automotive to aerospace. In many cases, they are used to make components that are too small or too fragile to be made by other manufacturing methods. Thanks to their high level of accuracy and repeatability, CNC turned components are often used in critical applications where failure cannot be tolerated.
For these parts, design considerations are critical to the success of the finished product. This post will discuss the five most important design considerations for CNC turned parts.
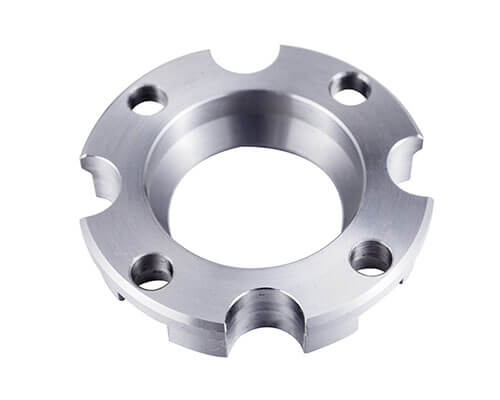
1. Material selection
The material used for a CNC turned part can greatly affect the overall design. For example, metals such as aluminum and brass are soft and malleable, making them easy to machine. However, they tend to be less strong and durable than harder materials like steel or titanium. To make the best choice, it is important to consider the application and desired properties of the part as well as the specific capabilities of the CNC turning process.
CNC machining materials must be strong enough to withstand machining forces, but also need to be resistant to heat and wear. In addition, the material must be compatible with the coolants and lubricants used in the machining process. Failure to select the correct material can lead to component failure, costly repairs, and even injury.
2. Tolerance
In any CNC turned part design, there are always hidden risks that can lead to a part that is out of tolerance. The causes of these risks can be varied, but can often be traced back to the design of the part itself. To minimize the risk of problems, designers must design with due consideration for machining tolerances.
If the size is too tight, the desired effect may not be achieved. If the dimension is too loose, the fit and function of the part may be affected. Therefore, a balance must be struck between these two extremes. The best approach is to use tolerances appropriate for the application. For example, tight tolerances are often used for precision components, while looser tolerances are more forgiving and help reduce costs.
3. Surface finish
Surface finish is an important factor to consider when considering the design of a CNC turned part. Achieving the desired surface finish can be a challenge, and the wrong choice of materials or tools can lead to poor results. Parts with a poor surface finish can experience a number of problems, including increased friction, excessive wear and loss of aesthetics.
Conversely, parts with a high-quality surface finish will run smoother, be more efficient, and look more attractive. When selecting a surface finish for a CNC turned part, it is important to consider the requirements of the application. For example, a rougher finish may be acceptable for interior components that are not visible, while a smoother finish may be desired for visible exterior components.
4. Threading and grooving
When designing precision CNC turned parts, it is important to consider threading and grooving processes. Threads provide a means of securing two components together by interlocking, while slotting allows for a smooth transition between two surfaces. When used in combination, these two features can help create more durable joints that can withstand higher loads.
Additionally, these features can be used to enhance the aesthetics of a part by hiding seams or creating interesting patterns. Therefore, incorporating these features into part design can help improve product safety, durability, and performance.
5. Wall thickness
Wall thickness is another factor to consider when designing CNC turned parts. If the wall thickness is too thin, the part may be fragile and prone to breakage. However, if the wall thickness is too thick, the part may be overweight and difficult to handle.
The ideal wall thickness for a CNC turned part depends on the material used and the required strength of the finished product. In general, however, a good rule of thumb is to keep the walls as thin as possible while maintaining strength and durability. By paying close attention to wall thickness, engineers can ensure parts are both strong and cost-effective.
Let Seicenc boost your business today!
Seicenc has been in CNC machining industry for 12 years, let us provide you with high quality custom precision machined parts.
By the end of 2022, we have worked with more than 1,000 clients in more than 30 countries, and supplied them over 1 million unique parts.
Do not hesitate. Just contact us right now! We will give you an instant quotaion within one days!