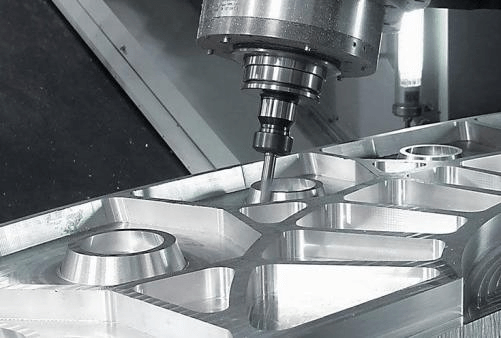
A CNC machine can complete small, simple parts with minimal supervision, but it needs help from experienced machinists to handle more challenging operations. When the workpiece is too big for the enclosure, or needs additional supports to prevent distortion, a creative machine shop can often find alternatives to complete the job in unexpected ways.
This article presents a few common challenges to machining large parts, and some potential solutions used by resourceful machine shops.
Table of Contents
Common Problems When Machining Large Parts

1. Working area not large enough
The range of motion on the equipment can’t reach everything that needs to be machined. Either the part is too large or the capabilities of the machine are too small.
Solutions:
- Work in segments. Machine everything in one area, then reposition the workpiece so that a new area is accessible. Custom jigs and stands can even be used to make sliding or rotating the workpiece easier and more accurate.
- Use different machinery. Machine shops have a wide range of equipment for completing specialized operations. In some cases, doing the work using different machinery with different capabilities is all that’s needed.
2. Too big for the enclosure
The workpiece is too tall, too long, too wide, or too bulky. Maybe there isn’t enough clearance under the tooling head, or the workpiece is too long to fit within the barricades on the machine. Perhaps the heavy workpiece exceeds the weight capacity of the equipment.
Solution:
- Break it down. While not possible in all cases, some parts can be broken down into smaller pieces. Operations may even be completed simultaneously on different machines to speed up processing times. This is best addressed during the part’s design phase.
- Alter the machinery. Can the tooling head be replaced with a shorter one to provide more clearance? Can barriers be removed to allow the parts to extend past normal limits? This approach can extend the capabilities of equipment, but extra planning is needed to prevent damage to equipment and parts. Consider using CAD tools to identify problems beforehand. Extra precautions may also be needed to ensure the safety of workers.
- Introduce external supports. If the part is unbalanced, it can cause tolerance problems. If the part exceeds the weight capacity of the equipment, it might also damage the equipment or present a safety hazard. Additional supports can take load off the machinery and stabilize the workpiece.
3. Does not meet design tolerances
After machining the part didn’t meet quality requirements for precision machining. Perhaps the workpiece wasn’t correctly repositioned by workers between operations, or separately machined parts don’t line up. Maybe the large, awkward part was difficult to secure and shifted during machining operations.
Solution:
- Take it slow. Spend extra time planning to prevent mistakes, and double check to make sure the workpiece is properly positioned and secured. While this increases process times, an experienced machinist knows the cost of labor and materials for rework aren’t worth the potential for a few minutes saved.
- Use semi-finish passes. Machining large parts takes extra care and patience. Particularly when tolerances are tight, taking an extra pass between roughing and finishing passes can help ensure precision and accuracy.
4. Distortion of features
When exposed to extreme heat and dynamic forces, parts can deform and become distorted. The high thermal stress from machining large parts can make the metal expand unevenly. If it is machined to design while expanded, it is likely to be outside tolerances once it cools. Additionally for a CNC lathe, a long, unbalanced part can introduce wobble by flexing out of position, resulting in a distorted profile and poorer surface finish quality.
Solution:
- Plan for expansion. Implement extra supports under vulnerable segments and ensure the workpiece is balanced to ensure precision.
- Manage heat input. Experienced machinists know that thermal expansion is an even bigger challenge on large parts. Machining large parts may require that you don’t remove as much material in each pass to reduce heat input. Also be sure that the right coolant is used and that it has good flow over the cutting area.
Rising to the Challenge of Large Part Machining
Large part machining is undoubtedly a challenge. The impacts of mistakes and inaccuracies are magnified, making them much more costly to remedy than they would be for smaller parts. And at least for the time being, computers and robots alone cannot cope with the nuanced challenges of oversized workpieces.
Machining large parts requires patience and careful planning, which may not be worth the risk to some machine shops. But it also presents an opportunity for top-tier machine shops to showcase their expertise and resourcefulness.
Seicenc has the capability to handle parts with a wide assortment of shapes, sizes, and materials. Just check our CNC machining services and let us know your requests. You can fill out the inquiry form to contact our sales team for more assistance.
Let Seicenc boost your business today!
Seicenc has been in CNC machining industry for 12 years, let us provide you with high quality custom precision machined parts.
By the end of 2022, we have worked with more than 1,000 clients in more than 30 countries, and supplied them over 1 million unique parts.
Do not hesitate. Just contact us right now! We will give you an instant quotaion within one days!