Finding the right CNC machining partner is not that simple. The perfect partner understands your needs, has the right capabilities and certifications in place, and always at a competitive price.
Let’s explore the ideal CNC machining manufacturer. The easiest way is to explore the six most important questions you should ask when evaluating potential partners.
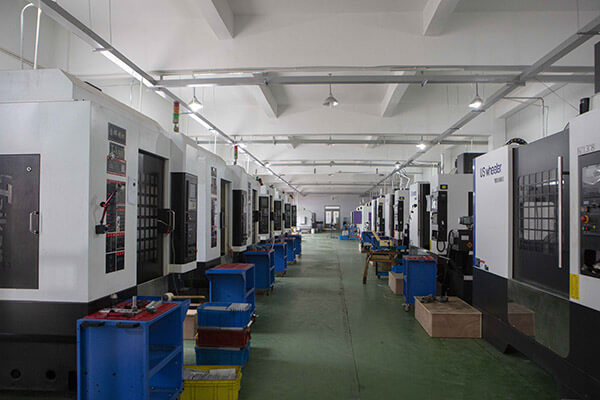
1. "What is the capability and scale of the CNC machining company?"
The ability to censor is obvious. Can a CNC machining company meet your current and future needs? High-end machining is only possible with state-of-the-art CNC machining equipment: CNC machine tools, CNC lathes, milling machines, robots and others.
Find out what casting materials this CNC machine shop can handle. What type of iron (gray iron, ductile iron, austempered ductile iron)? Aluminum? Steel or stainless steel? brass? bronze? Is there a reason the store doesn’t handle certain materials?
While capability is valuable, size does matter. You need to make sure that the CNC machine company has the capabilities to meet your needs. Clearly, a company increasing its capabilities or expanding its facilities is a sign of progress, as well as its ability to take on large projects and meet client needs. Just know your needs ahead of time.
2. "What customers and industries do you serve?"
It’s a good sign when a machine shop has experience in various trades. It shows flexibility and a willingness to take on unfamiliar projects. Additionally, it could mean that CNC machine shops can run complex parts with high cycle times just as easily as they can run less complex high-volume parts.
Ask specifics and listen to industries that require high performance components such as agriculture, construction, military, industrial equipment and automotive. If professionals in these industries are successful with this CNC machine builder, you may be too.
Finally, ask about the store’s first-degree relationships. There’s nothing like peace of mind knowing the store has extensive direct OEM/ Tier 1 customer interaction.
3. "What certifications do you have?"
Ability? Check. Recent growth? Check. All walks of life? Check. So far, so good. Another quality check that every machining supplier dealing with complex challenges should pass is having an ISO 9001-compliant quality management system (QMS). In addition, the IATF 16949 standard – designed to complement and be implemented alongside ISO 9001:2015 – helps ensure that products consistently meet requirements and quality is regularly improved.
4. "Can you source castings?"
High-end CNC machining companies value and respect the casting process; knowing that without casting, many complex metal commercial and industrial products would be too complex and expensive to produce.
Speaking of cost, did you know that design decisions account for 70% of a product’s manufacturing cost? Discussing the machining and casting requirements and cost of a part during the casting design phase is critical. A strong partnership between the CNC machine shop, customer and foundry provides cost-effective input into casting or machining designs.
A respected machining partner should be able to help you compare the pros and cons of different types of forming processes. Seeking strong, long-term relationships with a number of quality foundries, this means customers enjoy reliable supplies and meet deadlines.
Find a CNC machining manufacturer with a supply chain. If that shop manages the OEM relationship and simply delivers the complete machine part, your life will be much easier and you will have no worries.
5. "Do you have an in-house engineering department?"
A helpful engineering team – with many professionals with varying expertise – is involved in the early stages of projects to help develop the best possible parts efficiently and cost-effectively. The expertise these individuals bring helps manufacture designs and create trusted partnerships between customers, CNC machine builders and foundries.
A quality in-house design team can deliver designs/tooling quickly and cost-effectively, and can quickly prototype for foundry and machine tool projects. Additionally, an excellent in-house engineering department has a continuous improvement team that stays on top of the latest technology, identifying applications that can benefit customers.
6. "What makes you unique?"
This open-ended question seems unlikely to differentiate one store from another, but the answer you get should tell you something. That’s what you want to hear.
“Tolerance.” Different materials and processes refer to different standards. Your CNC mill builder should value how its precise craftsmanship meets tight tolerances to meet customer requirements and specifications. It is also important to be aware of the association’s guiding standards.
“Quality Control.” While all reputable CNC machine shops inspect parts, some go a step further by combining the expertise of their employees with automated audits to ensure consistency and accuracy. Some examples: CMM inspection, Millipore testing, custom gages, high precision bore gauges, hardness testing, surface finish testing, and roundness testing. The best quality control is error prevention, so ask about poka yoking, which can eliminate errors in machining and ensure quality parts.
“Our people.” Okay, that sounds cliche, but notice why people are so valuable. When you hear phrases like “better communication,” “cultural fit,” “good collaboration,” “schedules and deadlines,” and “customer feedback,” it lets you know your goals That’s their goal. And, because they are valued partners, they are more than willing to work hard for you and give you extra attention.
Let Seicenc boost your business today!
Seicenc has been in CNC machining industry for 12 years, let us provide you with high quality custom precision machined parts.
By the end of 2022, we have worked with more than 1,000 clients in more than 30 countries, and supplied them over 1 million unique parts.
Do not hesitate. Just contact us right now! We will give you an instant quotaion within one days!