The machine shop contains a variety of equipment to meet the production needs of designers. The machines can be used together to create an unlimited number of unique shapes for both simple and complex parts. However, without machining expertise, design engineers may not understand the capabilities and limitations of different kinds of CNC machining equipment. This can lead to unexpected inefficiencies and increased manufacturing costs.
This article will explain the difference between 3-axis and 4-axis CNC milling machines. The biggest difference between these machines is their ability to manipulate parts. By understanding how 4-axis CNC milling differs from 3-axis milling, designers can better predict the equipment needed to efficiently manufacture parts.
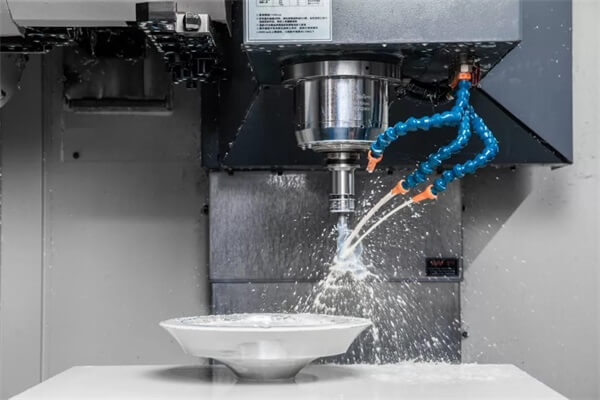
What is 3-Axis CNC Machining?
CNC machining almost always relies on a Cartesian coordinate system to define its positioning and motion. That means x-axis, y-axis and z-axis. The most basic milling equipment on the market is capable of 3-axis machining along these axes.
This means translational movement or sliding in only 3 directions: side to side, front to back, and up or down. We define these directions as x-axis, y-axis and z-axis respectively.
While 3-axis CNC machines can simultaneously combine motion along different axes to create curved shapes, they are somewhat limited in their capabilities. Parts with multiple side features require manual repositioning and realignment between operations, which slows things down. Workpiece repositioning, which may also be essential for features such as angled grooves, can be simplified and accelerated through the use of individually designed fixtures.
More complex features that include curvatures outside of a single xy plane are not even possible on a 3-axis milling machine. For example, a helical groove or the lobes of a camshaft. This means that 3-axis CNC mills are best suited for simple operations like drilling holes or milling slots.
What is 4-Axis CNC Machining?
A 4-axis CNC mill is capable of all the same movements as a 3-axis mill, but adds an extra axis of rotation called the A-axis. The 4th axis coincides with the x-axis for left and right movement. This means the A-axis allows the workpiece to roll forward or backward from the operator’s perspective.
While most 3-axis mills have a “flat” table for mounting parts, 4-axis CNC machines use chucks, panels, or vertical fixture blocks. Chucks and panels grip individual parts from the sides and can then be rotated 360° to access all sides. Tombstones house multiple components simultaneously for mass production.
The A-axis is useful for continuous movement of circular features or through indexing to reposition and then fix the part at a new angle. Either way, a 4th axis adds additional functionality and improves efficiency for parts that need to be machined on multiple sides.
Is 4-Axis Machining Better?
While small, simple machining jobs may require only a 3-axis CNC machine, a 4-axis CNC is sometimes preferred for three reasons:
A 4th axis adds the ability to machine more complex features.
When machining multiple faces, 4-axis CNC mills increase efficiency by eliminating the need for workers to reposition and realign parts.
Repositioning parts on a 3-axis CNC can introduce errors and affect the ability to meet design tolerances.
There are also 5-axis CNC machines available to further increase the allowable complexity of machined parts.
Seicenc uses a full range of high precision machining equipment to manufacture the parts you need with very tight tolerances. Check out our CNC Services page to learn how we can help you bring your next product design to market.
Let Seicenc boost your business today!
Seicenc has been in CNC machining industry for 12 years, let us provide you with high quality custom precision machined parts.
By the end of 2022, we have worked with more than 1,000 clients in more than 30 countries, and supplied them over 1 million unique parts.
Do not hesitate. Just contact us right now! We will give you an instant quotaion within one days!